What We Learned From the 2021 Supply Chain Bottlenecks to Maximize Efficiency in Operations Today
In quarter four of 2021, a large freight shipping port outside of Los Angeles was experiencing supply chain disruptions/bottlenecks that caused delays for operations around the Nation. There were 96 loaded cargo ships waiting at the port by December 2021. With about 40% of U.S. imports going through these docks, it caused a major shortage of inventory, and even consumers felt the distress.
There was a lack of labor paired with overwhelmed, overloaded supply chains – and the cost was significant. This is not the only supply chain bottleneck the industry was facing – China, Britain, Germany, and other parts of the world were experiencing similar delays at shipping ports. As we enter into quarter two of 2022, experts still believe that these bottlenecks will take more time to resolve to “operating as usual.”
Now more than ever, manufacturers need to become more resilient and adaptable with their operations. Therefore, it’s essential for business owners and logistics managers to look at their own processes and analyze bottlenecks within their supply chain to automate, adapt, and prevent future supply issues.
What are Bottlenecks?
In operational business terms, a bottleneck (or manufacturing blockage) is a part of your process that causes a delay in the system, which reduces the overall output.
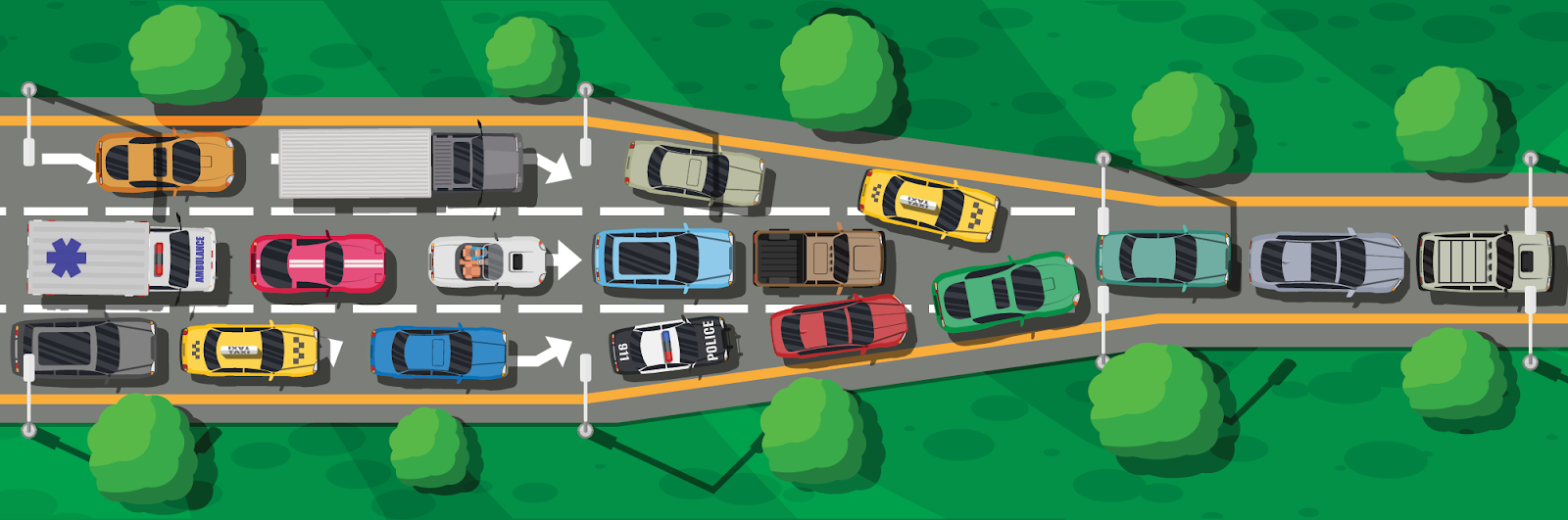
If you recognize bottlenecks in your system, identifying and analyzing them is essential to running your production processes more smoothly. If bottlenecks are not addressed, they can result in a loss of revenue, time, quality, and even customers.
Short-Term & Long-Term Bottlenecks
Short-term bottlenecks occur for a momentary period of time. For example, short-term bottlenecks can be caused by an employee being out sick for a few days, a machine needing repairs, or another temporary, short-term reason.
Long-term bottlenecks, however, cause prolonged operational flow issues that may reoccur until they are addressed. These bottlenecks can be generated by inefficient machinery or technology, limited resources, time-consuming manual processes, lack of labor or training, or the inability to adapt to quicker operations to meet consumer demands. When analyzed, long-term bottlenecks can improve the speed, accuracy, throughput, and customer satisfaction of an organization.
What Businesses Can Learn From Struggling Supply Chains in 2021
The shipping industry and supply chain bottlenecks in 2021 showcased how important it is to have a resilient supply chain that can adapt to sudden changes. Here’s how the 2021 bottleneck issues impacted the entire supply chain industry:
Labor Shortages
The pandemic resulted in a lack of labor – both domestically and internationally. This could have been caused by several reasons, including financial strain leading to job losses, health concerns, or the rise in e-commerce products which caused an increase in demand for workers. To address this issue, businesses needed to find ways to incentivize and attract more people to work in their operations. Higher wages, increased safety, and training and development opportunities were implemented in many organizations.
Consumer Behaviors
There were two significant changes in consumer behavior over the past three years; the increase in shopping online and the expectation of quicker or same-day delivery. To meet consumer demands, businesses need to be able to adapt their operations and processes quickly. Many companies invested in automated solutions and newer technologies. Others worked with multiple suppliers to always keep up with the need for increased inventory levels.
Shipping & Delivery
Shipping and delivery systems were overwhelmed by the increase in demand. This led to delays in the receipt and output of goods, which hindered customer deliveries. As a result, businesses invested in more robust shipping and delivery systems and micro-fulfillment solutions to address the issue. They also found new ways to communicate with consumers, offered expedited shipping options, and looked into multiple shipping providers.
Prices
In 2021, the cost of goods went up about 20% on average. This is not the first time we’ve seen a supply chain bottleneck that resulted in an increase of prices, but it is one of the most recent and significantly large-scale industry events. In 2013, a similar supply chain price increase was paired with a shortage in grocery goods.
Typically, demand rises due to the lack of inventory supply, and the price of goods increases in response.
Improve Your Bottlenecks & Processes With Automated Solutions
Analyzing bottlenecks in your current business operations can address throughput errors and increase customer satisfaction.
Are bottlenecks in your supply chain preventing you from reaching your business goals?
By investing in automation and technology, improving forecasting and planning, and increasing inventory levels, businesses can become more resilient and adaptable to meet consumer expectations.
McMurray Stern offers efficient automated storage and retrieval systems (ASRS). Our ASRS products help you store and retrieve materials with improved accuracy and speed to reduce bottlenecks and improve your operational flow. Here are some of the automated solutions we offer:
Micro-Fulfillment
Micro-fulfillment is a strategic customer shopping experience that gets products closer to the customer by allowing for on-demand delivery and cutting the distance between the warehouse and the customer’s front door.
HAIPICK Robot
The HAIPICK robot can replace the repetitive, time-consuming, and heavy manual storage and handling work, offering flexible customization, increased efficiency by 3-4x, and rapid ROI.
VLM
Vertical Lifts Modules (VLMs) are the ideal storage solution for industrial products in various industries. They help organize and improve work-flows and have a superior design for ease of use.
Carousel Systems
Carousel systems enable efficient storage and picking processes in the smallest possible space. As a result, carousels are an outstanding solution for handling small parts and medium to slow-moving products.
Shuttle Systems
A shuttle system is an innovative and economical solution to level utilizing pallets, trays, cartons, and bins if you need optimized storage with rapid material transport and quick access times.
McMurray Stern’s solutions can help you strategically design streamlined, automated processes in your warehouse and at the store level to help stay ahead of your supply chain for the future. To learn more about how to implement automated storage solutions into your operations and grow your warehouse, contact us!
Recent blogs
Explore Our Top Articles And The Latest Storage Trends, Where Industry Expertise Meets Innovation.